无溶剂干法复合加工中应关注哪些问题
http://www.packltd.cn 时间:2019年6月27日 关注数:969 次 |
摘要:在试验或生产过程中,如果下机时复合膜上有白点,该无溶剂胶水就会被认为不适用于该复合机的加工条件或质量不好。
在无溶剂干法复合加工过程中,白点是一个被普遍关注的问题。
在试验或生产过程中,如果下机时复合膜上有白点,该无溶剂胶水就会被认为不适用于该复合机的加工条件或质量不好。
关于无溶剂干法复合过程中的白点问题,建议从以下角度进行分析处理:
一、白点的实质
白点的实质:
与白点相对应的位置上,两层薄膜间存在空隙,薄膜没有被贴合到一起。
二、存在空隙的原因
a)涂胶量不足。载胶膜上局部无胶或胶量不足。
b)涂胶量不足。对应的涂胶量不足以填充油墨层上的“凹坑”。
c)涂胶时,胶水的粘度偏大,涂胶后,形成了较大的、凸起的“胶点”。
d)复合压力偏小,不能将凸起的“胶点”“压平”。
e)复合压力偏小,复合辊温度不够高,不能使薄膜发生充分的“变形”,使两片薄膜发生充分的接触。
三、相应的原因与处置方法
a)涂胶量不足,载胶膜上局部无胶或胶量不足。
1,此种情况通常与承胶辊、转移辊“不干净”有关,即承胶辊、转移辊上有未清理干净的胶体,从而导致局部的上胶量不足。
2,承胶辊上未清理干净的胶体导致在复合膜上形成“线条状”的“白点”。
3,转移辊上未清理干净的胶体导致在复合膜上形成“斑点状”的周期性的“白点”。
4,处置方法:
彻底清理涂胶单元的每一支辊。
b)涂胶量不足,对应的涂胶量不足以填充油墨层上的“凹坑”。
1,情况一:
油墨层,尤其是白墨层中的颗粒较粗,形成了较严重的凹凸不平的表面,所涂的胶量不足以填充墨层中的“凹坑”。
2,情况二:
印刷时,稀释剂中使用了过多的“假溶剂”,使墨层形成了较严重的凹凸不平的表面,所涂的胶量不足以填充墨层中的“凹坑”。
3,处置方法:
适当增加上胶量,同时适当增加复合压力。
c)涂胶时,胶水的粘度偏大,涂胶后,形成了较大的、凸起的“胶点”。
1,下图是胶水从涂胶辊转移到载胶膜的瞬间,图的下半部分描述了胶体从涂胶辊转移到载胶膜的过程。
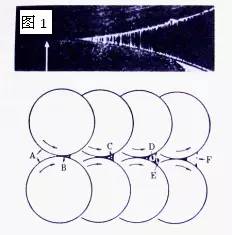
B点是涂胶辊上的胶体与载胶膜相接触;
C点是涂胶辊转动一定角度后,涂胶辊与载胶膜间的胶体被延伸,并在被延伸的胶体中形成一定量的“空洞”;
D点是随着涂胶辊的旋转而继续扩大的“空洞”;
E点是在涂胶辊与载胶膜之间已被拉成丝状的胶体;
F点是被拉断的“胶丝”。
2,在F点被拉断的“胶丝”,受胶体自身粘弹性的作用会迅速地“收缩”到载胶膜的表面,形成类似于“牛粪”的“胶点”。
该“胶点”的高度及经过复合辊后可被“碾平”的状态就与该无溶剂胶粘剂的结构设计及加工过程中胶体的温度有很大的关系。
3,下面的三张照片分别是在150米/分、220米/分和300米/分的速度下的无溶剂胶粘剂涂胶状态。很显然,在相同的温度条件下,设备运行速度越快则涂胶状态就越差。
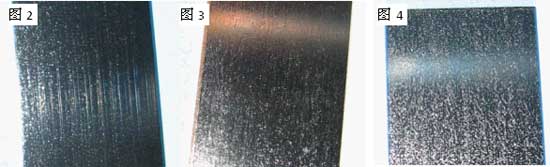
4,处置方法:
涂胶单元及胶体的温度应随着复合速度的加快而提高。
d)复合压力偏小,不能将凸起的“胶点”“压平”。
1,上述的“涂胶状态随加工速度加快而变差”的情况是一种客观存在,如果从涂胶单元到复合单元的距离足够长的话,胶体还是有机会“自然流平”的。
不幸的是,现有的无溶剂复合机的从涂胶单元到复合单元的距离都是比较短的,没有足够的时间让胶体“自然流平”。
因此,借助复合单元的压力和温度将胶体“碾平”就成为一种必然的选择。
2,所以,如果在低速情况下没白点,在高速情况白点严重的状态下,一方面说明胶体的流平性不足,另一方面就说明无溶剂复合机的压力不足!
3,处置方法:
适当增加复合单元的压力!
e)复合压力偏小,复合辊温度不够高,不能使薄膜发生充分的“变形”,使两片薄膜发生充分的接触。
1,在正常印刷条件下,非专色墨的墨层厚度应一微米以下,专色墨(包括白墨)层的厚度会在一微米以上,即在微观层面上,印刷品的油墨层表面是“严重的”“凹凸不平”的(如图5中的绿线所示),某些部位的墨层厚度可能只有一微米多(单纯白墨层处),某些部位的墨层厚度可能在三、四微米甚至更多(多层油墨叠加处)。
而在无溶剂干法复合加工中,上胶量一般都在2克每平方米以下,胶层的厚度小于2微米。由于没有像溶剂型干法复合机的平滑辊那样的装置使胶层在印刷膜表面进行“二次分配”,因此,涂在印刷油墨层表面的胶层也必然是“凹凸不平”的(如图5中的红线所示)。
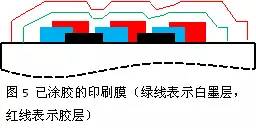
2,如果在高速条件下运行无溶剂复合机,由于胶层没有充分的时间自然流平,在复合压力不足的条件下,复合上去的第二基材状况就会如图6所示,保持原有的平直状态,并在胶层的“凹陷”处显示出“白点”的存在。
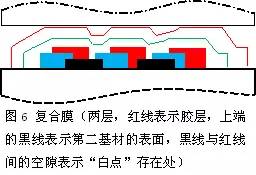
3,如果要在下机时就不让白点出现,就必须让第二基材在经过复合辊的瞬间发生充分的变形,一方面使涂好的胶层发生“滑移”,充分填补墨层中的“空隙”,另一方面,借助薄膜自身的变形以填补胶层的“凹陷”处。
4,基材发生物理变形需要两个条件:一是压力,二是温度。温度是使基材薄膜软化变形的必要条件,压力是使基材薄膜变形的充分条件。
5,如果基材的温度足够高(如使用第二基材的预热辊),则可以使用较低的复合压力。反之,则应尽量提高复合辊的压力。
6,如果设备的运行速度较高(例如400米/分),由于复合膜在复合单元处停留的时间相对较短,基材与胶层受压变形的时间也比较短,因此,就需要使用更高的复合压力。
1000千克每延长米的复合压力也许是最低值。必要时,应以复合单元气缸压力表值的80%为施压的上限(例如,复合单元气缸压力表的最大值为1MPa,则允许使用的最大压力为0.8MPa)。
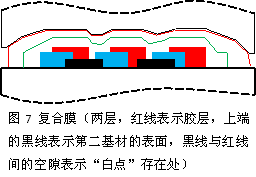
备注:
1,在无溶剂干法复合过程中,下机时也会出现如下图所示的“气泡”现象。经检查,是由于复合辊(钢辊与胶辊)上附着的污物过多所致。将复合单元清理干净后,“气泡”问题消失。
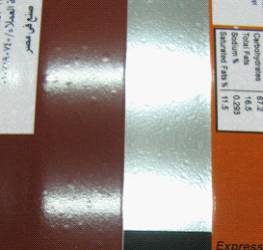
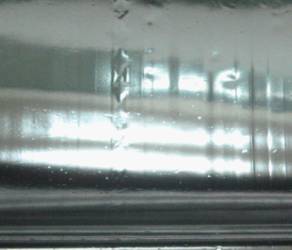
2,涂胶单元各辊的温度也应关注。
如果操作侧与驱动侧的温度值有明显差异的话,会对复合产品的外观产生明显的影响。造成两侧温度不一致的原因是热媒(水或油)的流量不足。造成流量不足的原因是管路堵塞或循环泵故障。
(来自:包装企业网)