关于无溶剂复合的八个控制要点
http://www.packltd.cn 时间:2019年2月26日 关注数:5091 次 |
摘要:固定辊、计量辊、涂布辊、涂布压辊、复合钢辊、复合压辊、混胶导管、混胶机的主剂和固化剂桶以及各个导辊,都必须要做到清洁无异物,因为这些部位只要有一点异物,复合膜表面就会有气泡、白点现象出现。
一、清洁
做好无溶剂,首先要做到的必须是清洁,这也是极易被企业忽视的一点。
固定辊、计量辊、涂布辊、涂布压辊、复合钢辊、复合压辊、混胶导管、混胶机的主剂和固化剂桶以及各个导辊,都必须要做到清洁无异物,因为这些部位只要有一点异物,复合膜表面就会有气泡、白点现象出现。
二、温度控制
无溶剂胶水主剂是异氰酸酯聚合物(通常叫NCO成分),固化剂是多元醇聚合物(通常称之为OH成分)。主剂和固化剂的密度、粘度、性能以及胶水的使用寿命、使用温度、熟化温度和时间等因素都会影响复合质量。
一般的胶水供应商都会给客户一些使用参数作为参考,其中使用温度一般给出的是一个范围值:使用温度越高,胶水的使用寿命就越短,粘度也就会越高,胶液就会变白或胶液气泡变多,这时涂布电机的电流表就能看出相应地增大了。所以企业需要根据自身设备的实际情况调节出最佳的使用温度。
国内大部分的无溶剂胶水粘度在2000 mpa`s/25℃以下,在涂布辊上的温度控制在30~35℃左右。而国外的无溶剂胶水由于粘度比较大,为了更好的流平性,涂布辊的温度要适当增加3~5℃。这就需要复合师傅能充分地了解每家胶水的特性去做对应地调整。
计量辊、涂布辊的温度调整主要看胶黏剂粘度的高低,粘度越高的胶水计量辊的温度要相应提高,复合热辊的温度一般可控制在50±5°左右。
三、上胶量控制
根据复合基材的不同,可以使用不同的上胶量,如下表:
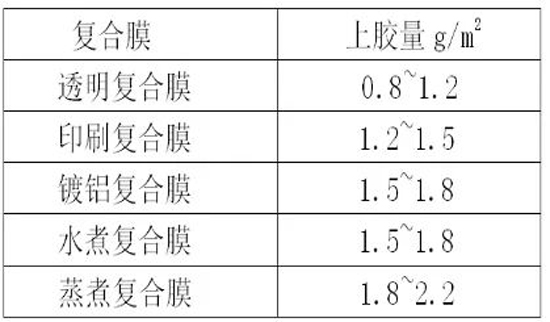
表格中给的是上胶量的大致范围,而生产中上胶量的控制主要是由计量辊与固定辊的间隙和转速比来决定的。拿诺德美克无溶剂复合机来讲,它的计量辊间隙是80um时,基本上胶量是:
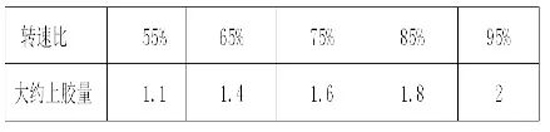
所以复合生产时,合适的、真实的上胶量需要我们多次检测样品膜和批量生产来确定。上胶量严重不足时,会出现大量的气泡、剥离强度不好等问题,但这并不表示上胶量越大就越好,上胶量如果过大时,就会出现复合膜两端溢胶,或者复合膜有桔斑状现象(透明度不好)。
四、张力控制
张力的控制在无溶剂复合当中相当重要,因为无溶剂复合它的初粘力相当低,如果前后膜的张力不匹配,在熟化的过程当中就有可能由于膜的收缩不一样造成表观气泡和隧道的现象。
一般尽可能把第二放料放小一点,比较厚的薄膜要适当增加张力和复合热辊的温度。尽可能做到复合下来的薄膜不能有卷曲现象。锥度的张力控制也是至关重要的,要随着薄膜的厚度相应地调整。
五、压力控制
由于涂布辊是靠两根光辊的间隙和转速比来控制上胶量的,所以涂布压力的大小会直接影响上胶量(特别是流平性比较好的胶水),压力越大上胶量就越小。复合辊处的压力对质量的影响,我们可以用中高辊和平辊来做对比试验,材料结构OPP/VMPET,速度300m/min,结果如下:
1、平辊复合熟化以后,复合膜靠中间部位明显有白点、气泡现象。
2、用中高复合胶辊的复合膜熟化后未见白点、气泡。这是由于无溶剂复合机基本宽幅在1.5m以上,所以用平复合胶辊,两端压力能满足所需要的压力,而中间部位的压力就明显不足,所以这就是压力问题带来的气泡、白点。
六、油墨与胶水匹配性
现在的无溶剂胶水与醇溶油墨复合,就容易出现白点问题。与酯溶油墨的匹配性一般都比较好。
七、控制湿度
时常关注湿度的变化,要相应地调整主剂跟固化剂的比例。因为无溶剂复合速度很快,如果湿度太大的话,涂布好胶水的复合膜仍然会与空气中的水分接触,消耗掉部分异氰酸酯NCO,形成胶水不干和剥离不好等现象。
比如早晨上班时的湿度较大,就应该把固化剂OH的比例往下调。当湿度大于90%时,尼龙原则上不可以复合。
在夏季高温高湿天气时,要勤换空气干燥剂;胶水桶的密封性能(密封圈、胶液液面感应器处、桶盖要盖严实)、储气罐要安装排水阀、有条件的企业最好安装独立的无溶剂复合车间、安装去湿设备。
在操作时尽量减少往胶桶倒胶水的次数,如果能一次倒进就不要用两次,最好是一次把胶水桶盛满,使胶水桶里趋向于真空状态。
八、其他因素
复合镀铝膜时可适当把固化剂OH成分调高,这样对于镀铝膜的转移能起到一定的缓解效果。
对于内膜厚度大于60um的复合结构,适当降低固化剂OH的比例,可以提高复合膜的剥离强度。
遇上阻隔性强的复合材料要降低速度,例如PET印刷再复合VMPET,国内现在速度都难以超过250m/min;速度越快带入含水分的空气就越多,气体无法排出就会形成气泡、白点。
熟化温度越高,胶水的反应速度就快,一般的熟化温度控制在40℃以内,但熟化温度越高,复合膜相应的摩擦系数就加大了,因为温度越高,薄膜的助剂就会大量析出,造成摩擦系数的增大。
九、结语
无溶剂复合并不难,只要工人师傅们用心做好每一个细节,仔细观察每一道程序,就能做出高效、优质的产品。
(来自:包装企业网)