关于工作粘度对无溶剂复合全过程的影响
http://www.packltd.cn 时间:2020年5月12日 关注数:803 次 |
摘要:所谓数字式粘温特性,简单地说就是指数字化方式表征的胶黏剂粘度随温度变化的规律。
所谓数字式粘温特性,简单地说就是指数字化方式表征的胶黏剂粘度随温度变化的规律。如下表所示。
表 某典型双组分胶(A胶和B胶)数字化特性参数表
单位:mpa•s |
||
T1-A |
T1-B |
|
0℃ |
16200 |
3900 |
5℃ |
9940 |
2700 |
10℃ |
5600 |
1750 |
15℃ |
3400 |
1200 |
20℃ |
2100 |
800 |
25℃ |
1300 |
560 |
30℃ |
890 |
410 |
35℃ |
600 |
300 |
40℃ |
430 |
220 |
45℃ |
310 |
170 |
50℃ |
240 |
130 |
55℃ |
180 |
100 |
60℃ |
140 |
80 |
从上表可以看出,在不同温度下,两种胶液的粘度数据相差很大;而即使在同样温度下,两种胶液的粘度可以相差最高约4倍。
通过数字粘度我们可以很好地分析它对混胶、涂布和复合的影响。实践证明,其它影响程度远超出了大多数人的想象。下面分析提到的粘度实际上都是我们常常说的工作粘度。
一、粘度对双组分胶混合均匀性的影响
粘度对双组分混合均匀性的影响主要体现在两种胶液粘度值差过大时会无法实现均匀混合。
两种胶液粘度越接近,其混合均匀性越好。这是由静态混合管工作原理所决定的。
自动混胶机都有A胶和B胶的加热和温控系统,而且是相互独立操作和自动控制的,其目的就是将使两组分胶液的工作粘度始终控制在一个适当范围内,以便于充分均匀的混合。
但是,在现实生产中,混胶作业时常出现某些问题,究其原因主要还是与双组分胶的工作粘度偏离正常范围有关。
常见的不正常主要有两种现象:
1)工作温度设定不合理或设定错误
双组分胶厂家都会为用户推荐A胶和B胶的工作温度区间,二者独立且通常温度上下限都不一样的。实际生产时的问题可能是如下原因引起的:
首先,正因为A胶和B胶工作温度可独立设定,可能会留下某种隐患。虽然两者的设定值都在推荐范围内,但如果操作人员分别选定了极限值,实际两者的工作温度就不在优化区间,甚至可能已经偏离了稳定工作区。
其次,一般说明书都没有对什么条件下使用上限或下限做出明确规定。由用户根据经验确定,更没有工作粘度参考说明。对缺乏经验的用户可能出现更严重的设置错误,A胶B胶温度高低倒置,产生批量废品。
2)低温时节预热不充分导致混合时A胶和B胶粘度悬殊
在低温时节,我们强调要对胶黏剂进行充分预热。
如果是一种胶液工作温度达标而另一种胶液温度过低,就会出现因两者粘度相差过大,混胶不均匀,从而产生随机性局部不干的故障。
2018年,我们首次在业内提出了“等粘度混合”的概念,其目的正是为了消除双组分胶温度误设置和预热操作不到位等因素引起的各种不利影响。
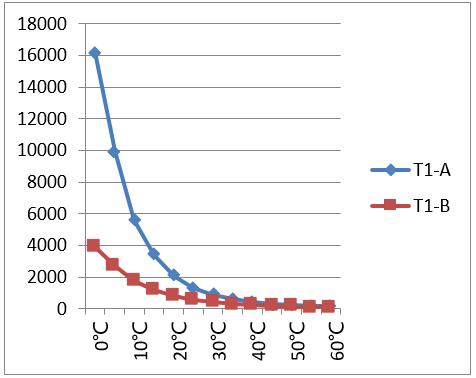
图 某品牌双组分胶(A胶,B胶)的粘温曲线
从上图可以看出,选择A胶和B胶的工作温度主要是依据图表中的水平线。因此每个品牌的合理工作温度都是不同的。
二、粘度对涂布状况和一致性的影响
胶黏剂的涂布粘度会影响转移率和涂布效果。
2018年,我们在C600智能型无溶剂复合机上首次提出了“恒粘度转移”的概念,正是为了减少或消除涂布单元胶黏剂因为粘度改变而导致的转移不良和涂布不均匀的不利影响。
等粘度混合和恒粘度转移是通泽为探索工艺数字化而提出两个新概念!
即使混合均匀的胶黏剂在涂布单元上也可能出现转移不良和涂布不均匀的现象。这种现象出现的原因在多数情况下也与胶黏剂温度异常导致其各种粘度异常有关。
辊筒表面温度不均匀,或者设定值与实际值相差明显,导致胶黏剂粘度与期望值不符,转移和涂布不良,是许多无溶剂复合机都出现过的现象。
辊筒表面温度不均匀大部分是横向不均匀(宽度方向不均匀),导致胶黏剂横向转移不良,严重时涂布基材上能看到诸多纵向线条。其主要来源有两种:
1)本身设计缺陷,主要加热系统和辊筒结构;
2)参数设置错误,比如没有根据环境条件调整加热机温度值,在环境温度很低时就出现辊筒两端温度偏低的情况,导致无法局部胶黏剂无法正常转移。
三、粘度对复合效果的影响
在这里,我们先要重新提到两个概念:涂布粘度和复合粘度。
涂布粘度是指胶黏剂在涂布时的工作粘度。
复合粘度是指胶黏剂在复合时的工作粘度。当然,这里指的涂布和复合分别是指基材经过涂布钢辊和复合钢辊的短时或瞬间。
如果复合粘度控制不好,涂布良好的基材也可能出现复合不良或复合强度下降。
发生这类现象的原因主要是复合粘度异常增高。大致有两种情形:
1)从涂布到复合通常要经过较长的通道,在这一段,基材表面温度会下降,导致其复合粘度增高。复合粘度增高通常有利于复合稳定性,但有时可能产生相反的效果(比如,不利于流平、需要更大复合压力压平等),取决于增高的幅度。
2)停机换料时,通道段基材表面胶层温度有时会明显下降、粘度升高,影响复合均匀性和强度。
随着无溶剂复合应用的推广应用,单组分胶的使用比例在不断增加。由于其采用高温工作温度(通常80-110℃)、运行速度也较低,上述情形的影响可能更为常见和明显,甚至会显著降低复合强度。在织物领域就出现过类似的实例。
四、粘度对收卷效果的影响
与涂布粘度、复合粘度相同,我们在这里还要引进收卷粘度的概念。
收卷粘度是指胶黏剂在收卷时的工作粘度。
一般人都不大会关注这一概念,因为从复合到收卷时间间隔很短,胶黏剂粘度改变不大。但是,当使用冷却辊或者环境温度低等情况下,收卷时粘度就会与复合时明显不同。
而从品质管理的角度看,收卷粘度及收卷状态恰恰是更重要的一个控制点。
有必要指出,混合的AB胶黏剂的粘温特性与两种单胶的粘温特性是不同的,这方面还需要进一步的专业研究。
总之,胶黏剂的粘温特性具有从预热、混胶、涂布、复合到收卷全过程的影响,是无溶剂复合的一个工艺关键因素和难题。它同时也为我们展示了下一步工艺优先、操作改进、设备升级的思路和方向。如果能在此基础上实现的数字化粘度控制,我们就有望获得优化的工艺条件和最佳品质的质量。
(来自:包装企业网)